For 30 years since the advent of the Purdue University Computer Integrated Manufacturing (CIM) Model, also referred to as the Purdue Enterprise Reference Architecture (PERA), manufacturing companies have thought of their business processes and supporting applications as a hierarchy – a pyramid – that starts on the shop floor and goes to the corporate executive offices. This manufacturing operating model has become the basis for most systems deployment strategies. See Figure 1. Now it might be time to challenge this assumption.
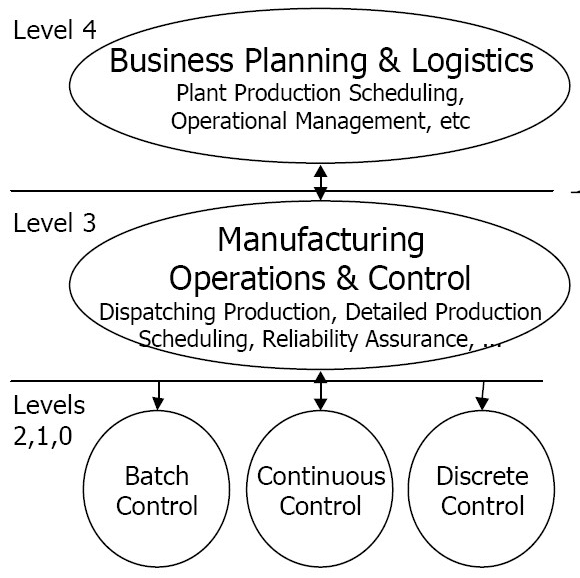
This hierarchical model has been cemented into manufacturing architecture with standards like ISA95, which has become the most common model defining shop floor application functionality. Conferences and symposia have featured numerous papers on “shop floor-to-top floor integration.” With the “if it isn’t broken, don’t fix it” mentality so common in manufacturing, the CIM pyramid looks like it may well stand as long and solidly as the pyramids of ancient Egypt. But, with the emergence of the Industrial Internet of Things (IIoT), Artificial Intelligence (AI), and the advanced analytics now available with a data anywhere and everywhere model, it may well be time for the CIM pyramid to get leveled.
The Appeal of the Pyramid
When digital technology came to manufacturing, it first appeared in the corporate finance and accounting systems. With the advent of integrated circuits, the digitalization of process control systems began in earnest. Next came the minicomputer and then the personal computer, which made computing on the shop floor practical. The differences in the openness, communications protocols, and programming of each type led to a natural stratification.
To promote the adoption of digital technology, Dr. Theodore Williams at Purdue University led a team that both examined the nature of this stratification as well as refined how technology was being deployed. He promoted a way to tie it all together to provide “computer integrated manufacturing” or CIM. Interestingly, the natural layers of the Purdue model also aligned well with the hierarchical organizational structures common in manufacturing in the 20th century. This natural alignment made the Purdue model easy to understand which is why it became so entrenched as a manufacturing operating model.
The Explosion of IIoT and AI Changes Everything for Manufacturers
In the last five or six years the rapid ascendance of wireless communications, smart devices, and anywhere connectivity, the Industrial Internet of Things (IIoT), and artificial intelligence (AI) have emerged as technologies that can effectively handle the vast amounts of data now being generated by manufacturers. The proliferation of IIoT devices has changed the manufacturing landscape and is now challenging the manufacturing operations model.
At the same time, geopolitical upheavals such as the coronavirus pandemic have forced manufacturers to rethink the way they do business. With work-from-home and social distancing restrictions, the idea of a rigid manufacturing operations model has fallen by the wayside. Organizations are striving to be more agile. The idea that all information must flow up or down a predefined path is no longer manageable. Instead, the long-sought-after concept of making available the right information to the right person at the right time is now an imperative. As operations continue to become more agile, peer-to-peer networks that are adaptive and agile themselves are emerging as a new best practice.
A Historical Perspective
We can look to the past to better understand why clinging to an existing model can inhibit modernization and change. In the 1800s factories were either powered by water wheels, turbines, or steam engines. These point sources of power resulted in factories that had a centralized power source which then utilized line shafts and belts to power all the machinery. It was then practical to compactly locate these as close to the power source as possible, resulting in cramped and often unsafe factories.
These factories also had to be located close to moving water either as the power source or for the steam engines. When the electric motor was first introduced, it simply replaced the existing single steam or water turbine. It wasn’t until engineers realized that multiple, smaller motors could eliminate the shafts and belts while improving plant safety.
The Emergence of an Alternative Manufacturing Operating Model
There are many parallels between electricity as a technology disruptor and what is now possible from the IIoT and advanced computing technologies. Manufacturers can now leverage vast amounts of data to gain insights and manage operations processes in different ways – previously not considered possible. The first stage of today’s digital transformation has been to simply replace components of an existing operating architecture. The next stage is to rethink how to better manufacture new products with greater value, for less cost.
Smart devices that operate anywhere are now empowering manufacturers to rethink the way they operate and maintain their facilities just as electricity did over 125 years ago. Where are you at with your business transformation – still in stage 1, or have you moved on to exploring new ways to grow your business or product suite? Will your manufacturing applications be able to support this new model or are they built assuming that the CIM pyramid will stand as long as the real ones have?