What Is Manufacturing Process Management?
Manufacturing Process Management (MPM) is an ideal application for paperless systems. It enables manufacturing engineers to model and assess the resource requirements of the product design, and then identify the production methods that will best meet cost, quality, and other goals.
Managing all of this with paper is ineffective at best. Paperless MPM is not only manageable but contributes significantly to company profits–especially when integrated with other digital solutions such as MES, MRO, SQM, and ERP.
Electronic Procedure
Systems: Vital to Paperless Manufacturing
Paperless systems open up new ways to make money in manufacturing, and electronic procedure systems for process management are a key step in going paperless. As the bridge between design and physical production, it sets the stage for the paperless processes that follow. It ensures that manufacturing plans are viable and effective, and that everyone has the correct work instructions at all times and in all places.
With MPM, everyone is on the same page with a single version of the truth from the start of manufacturing onward. Further, MPM lays the foundation for all the paperless processes that follow in the Manufacturing Execution System in addition to applications like Supplier Quality Management and Maintenance, Repair and Overhaul.
What Are the Benefits of Process Management Systems?
Standardization and Compliance
Continuous Improvement
Limit Discrepancies and Their Impact
non-conformance issues.
Reduce Unplanned Downtime
Facilitate Production Ramp Up
Model and Optimize
The Purpose Of Manufacturing Process Management
MPM defines the manufacturing process for a given design. It then distributes and manages specific process plans and work instructions to the various production teams. This includes all the activities associated with manufacturing: internal resources, partners and suppliers, and ongoing change orders. Because MPM involves so many people and functions, it has a significant impact on quality, productivity, and profits.
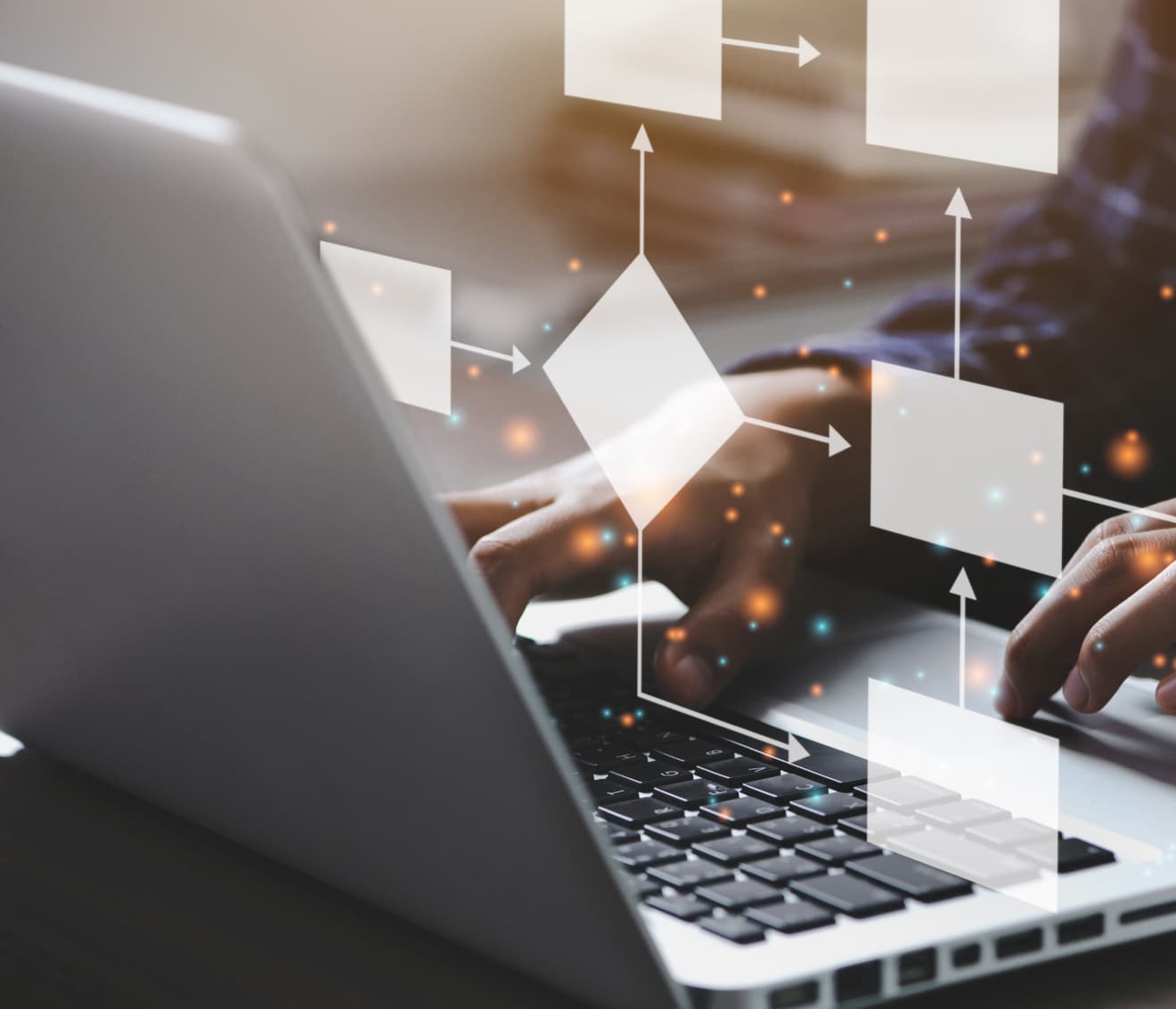
What Is a Manufacturing Process Definition?
The manufacturing process definition establishes the essential processes required to manufacture and sustain a product, from initial conception and design through lifecycle maintenance, repair and overhaul. It defines the overall characteristics of the processes to and the roles of suppliers, but the specific details–such as which supplier or production technique should be used–are left to the process plan.
An important part of the process definition is the assignment of supplier roles. When integrated with Supplier Quality Management (SQM), businesses can use MPM to network with suppliers, rate their service, and perform automated tests and inspections.
Using a system updated in real-time means better collaboration between internal and external players. MPM ensures that all parties are always working with the correct process plans and work instructions, avoiding the delays and costs that occur when there is not a “single version of the truth.”
What It Does – Process Plans and Work Instructions
Once the manufacturing process has been defined, MPM manages the creation of process plans and work instructions which are then distributed to shop floors for execution. Digital process plans and work instructions manage change and enforce consistent results on the shop floor.
Manage definitions and changes
Distribute revision-controlled work instructions to the shop floor
Manages revision-controlled work instructions with all where-used data stored for traceability
PLM or MES: Who Owns the BOM?
BOM management is crucial to refined manufacturing operations. It originates with product design engineers as an engineering BOM (eBOM), and is usually created and stored within a Product Lifecycle Management (PLM) system. A separate manufacturing BOM, or mBOM, must be created to guide specifics of sourcing and manufacturing/assembling. The eBOM and mBOM are distinct and each requires its own version of the truth.
While the mBOM can be created in other applications, it’s more seamless to maintain and execute manufacturing BOMs in the MES where it’s close to the activity on the shop floor and is in the best position to execute efficiently. That’s especially true when you consider there can be as-built, as-shipped, and as-maintained BOMs, all of which may vary considerably from the original eBOM.
MES is intended to manage this kind of manufacturing complexity, and Solumina by iBase-t is designed to easily integrated with your PLM/Engineering tools and your ERP/production planning and procurement tools.
Integrated MES And MPM: A Powerful Combination
A Manufacturing Process Management System does not operate alone. It is closely linked to everything that happens on the shop floor. That’s why integrating MPM within a larger MES solution is so powerful. MES and MPM together create a synergy that multiplies the value of each application.
Improved Closed-loop Capability
Efficient Change Management
Model-Based Manufacturing
iBase-t Makes Integration Easy
Integration doesn’t stop with MPM and MES. Working with CAD/PLM leaders such as PTC, Siemens and Dassault Systèmes, iBase-t has developed the bridges needed to integrate MES with PLM and ERP systems. We constantly evolve these bridges to incorporate newer standards for integration as they become natively supported by CAD/PLM vendors.
When You Demand Precision, iBase-t Delivers
Digital MPM is especially valuable in complex discrete manufacturing, which by definition involves complexities that are difficult to manage with paper systems. Manufacturers in this space often deal with hundreds or thousands of parts, iterative testing and improvement, frequent change orders and customization, internal and regulatory standards, and multiple teams collaborating from different locations.
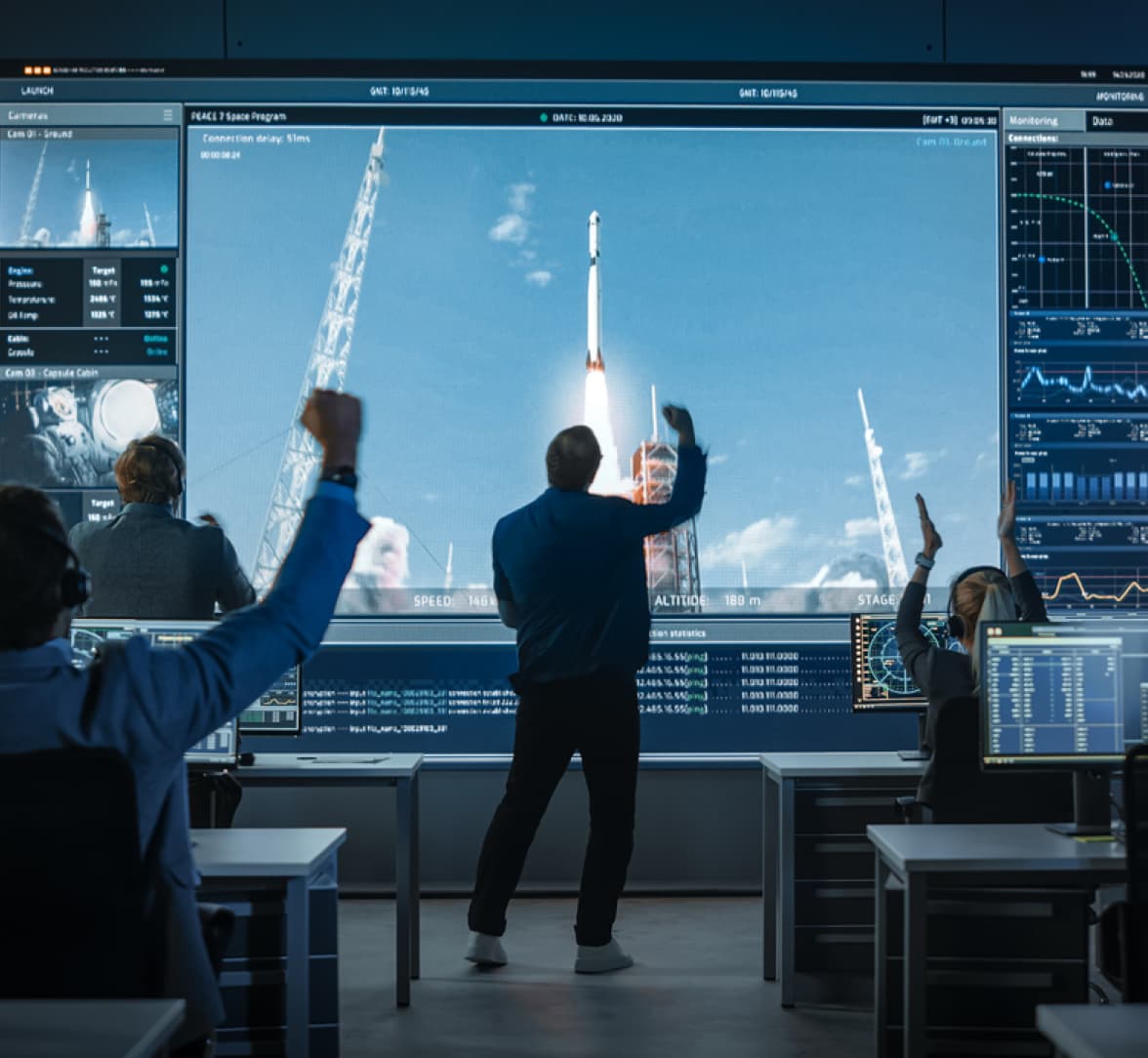
iBase-t. Your Partner in Intelligent Manufacturing
iBase-t specializes in highly engineered, complex discrete manufacturing environments. Our solutions are specifically designed to handle this complexity and provide the control needed to increase manufacturing efficiency, productivity, and profits. Contact our experts to learn more about how complex manufacturers can benefit from robust manufacturing process management software.
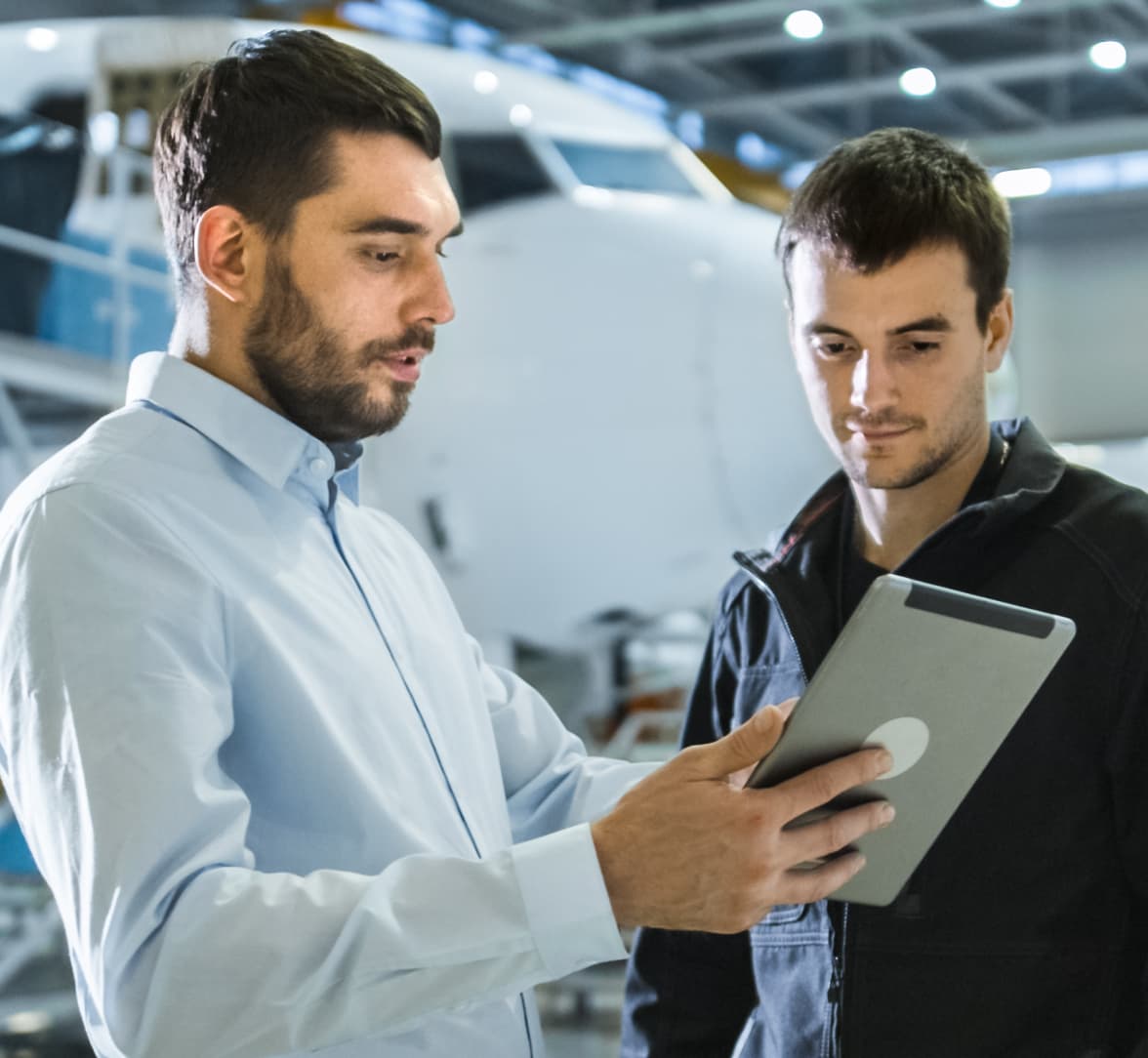
Stay Sharp with Razorleaf Podcast
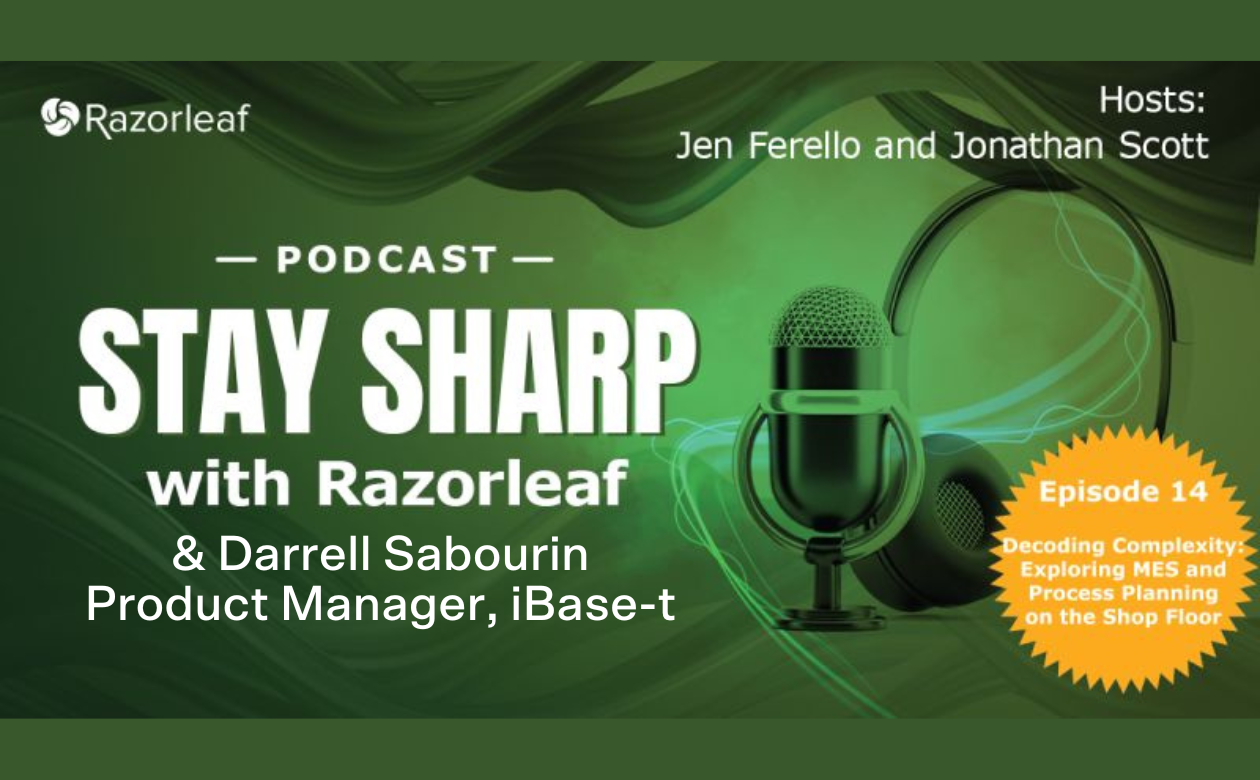
Stay Sharp with Razorleaf featuring Darrell Sabourin, Product Manager at iBase-t
Learn More About Manufacturing Process Management
Learn What Solumina
Can Do for You With a Custom Demo