Extend Quality Best Practices Across The Enterprise
In complex discrete manufacturing, rigorous quality, safety, and regulatory requirements leave little room for error in any stage of your process. iBase-t’s embedded Enterprise Quality Management System (EQMS) makes it possible to ensure products are manufactured to the highest quality standards on a consistent basis, while attaining manufacturing efficiency and performance goals in the process.
Ingrain Quality Management at an Enterprise Level
Solumina EQMS is embedded into our MES, MRO, and SQM solutions, integrating quality best practices into every process across the enterprise. Its goal is to ensure product meets customer requirements and standards, drives continuous improvement, and accelerates new product introduction. Key activities include quality inspection and test plans, closed-loop CAPA processes, compliance documentation, and more.
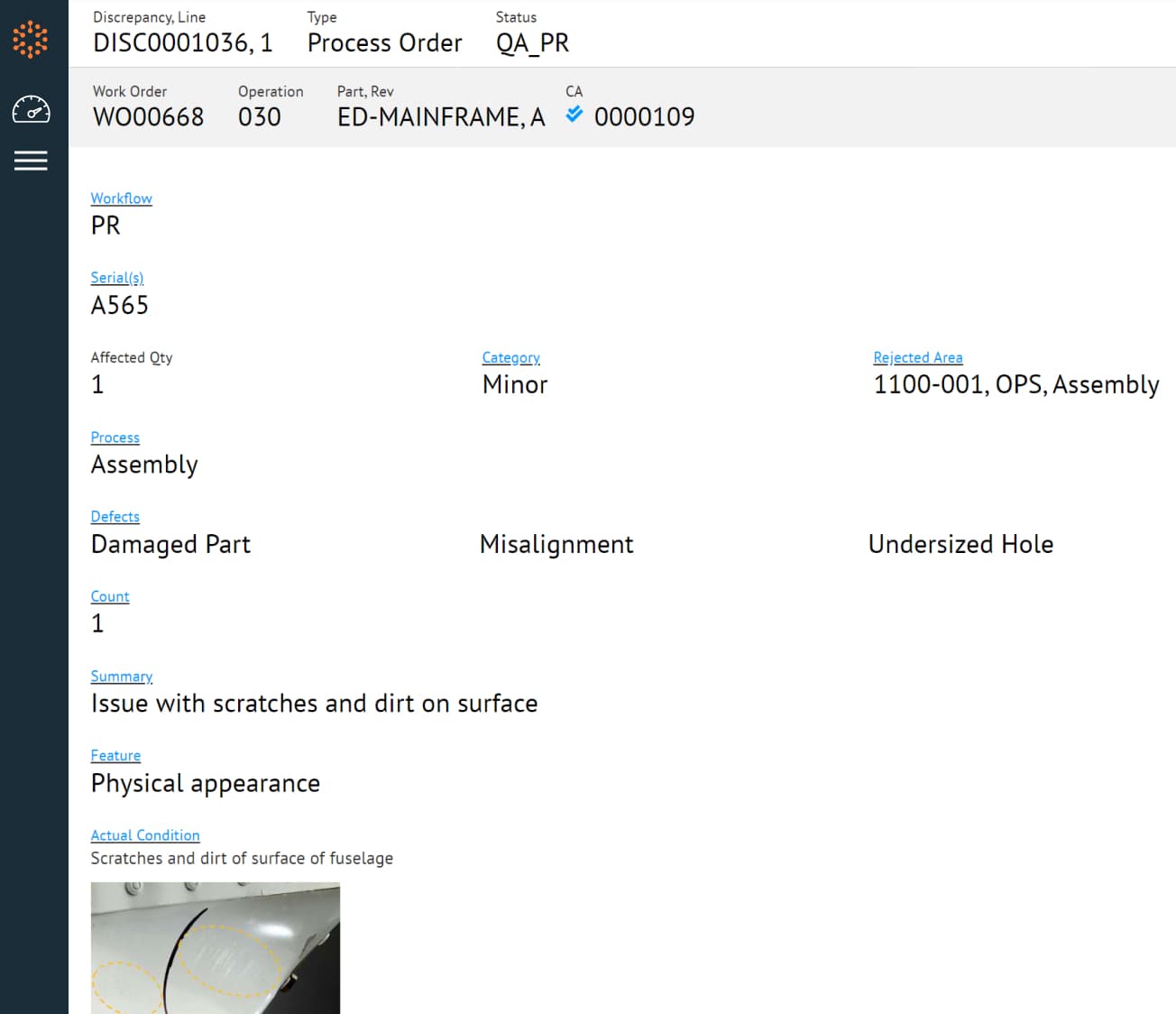
Standardize Quality Management and Enforcement
Standardize and integrate quality planning, execution, and discrepancy management with every production process to improve quality and efficiency.
Inspections
CAPA Management
Discrepancies
Process Control
Product Control
Compliance History
“With Solumina EQMS, you can shine in every aspect of quality management, including supplier collaboration, production performance, and MRO.”
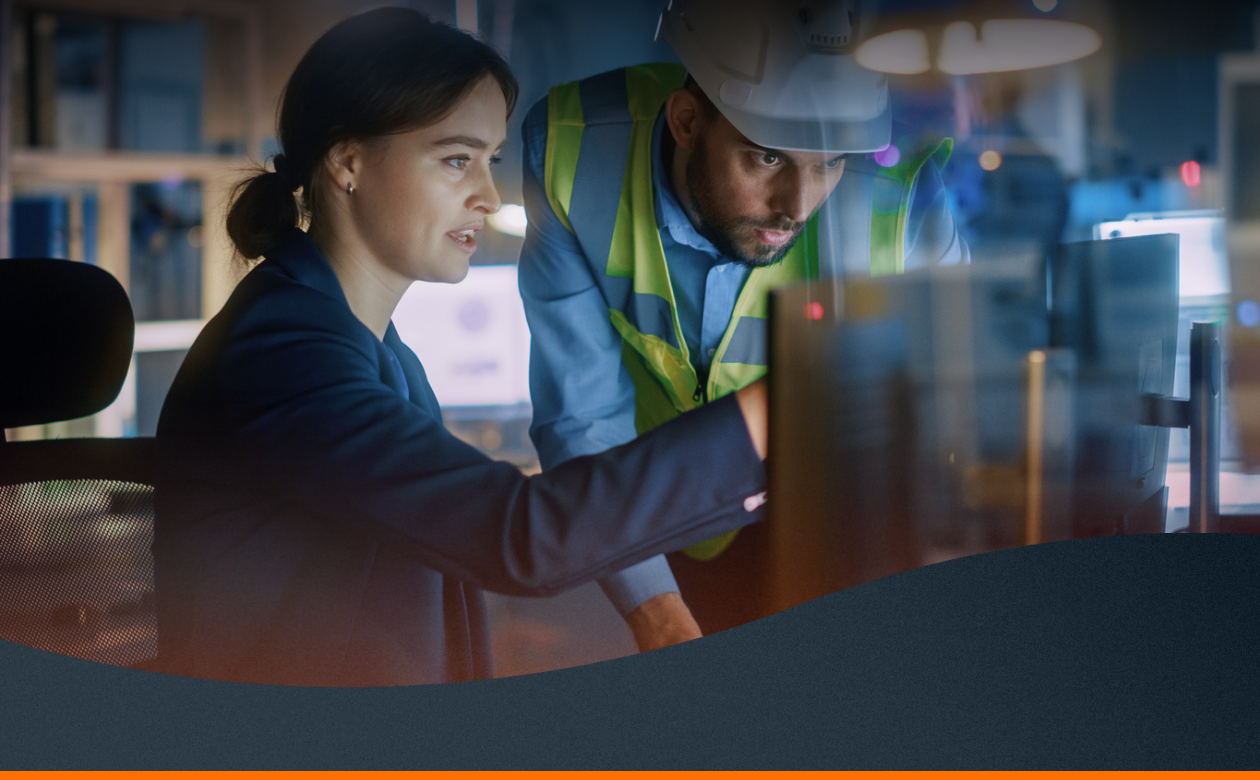
Solumina EQMS Brochure
See how with Solumina EQMS, you can shine in every aspect of quality management, including supplier collaboration, production performance, and MRO.
Manage and Act
On Every Aspect of Quality
Visibility, efficiency, and control.
Complex discrete manufacturers must manage quality in multiple dimensions – from discovering and tracking defects to identifying and issuing corrective actions to the right stakeholders at the right time. With EQMS, you can shine in every aspect of quality management, including supplier collaboration, production performance, and MRO.
Ensure 360° Visibility and Compliance
Accelerate Without Sacrificing Quality
Reduce the Cost of Quality
Make Better Decisions
Control Change Procedures
Streamline Your Process
Learn To Redefine Quality Management Standards
Learn What Solumina
Can Do for You With a Custom Demo