Competing in a Highly Regulated Industry
The medical device industry combines the complexity of highly engineered products with multiple, stringent regulatory requirements, in a market where failures can be catastrophic. Solumina from iBase-t is designed for this kind of challenging environment, helping you maintain quality, meet regulatory compliance and stay competitive at the same time.
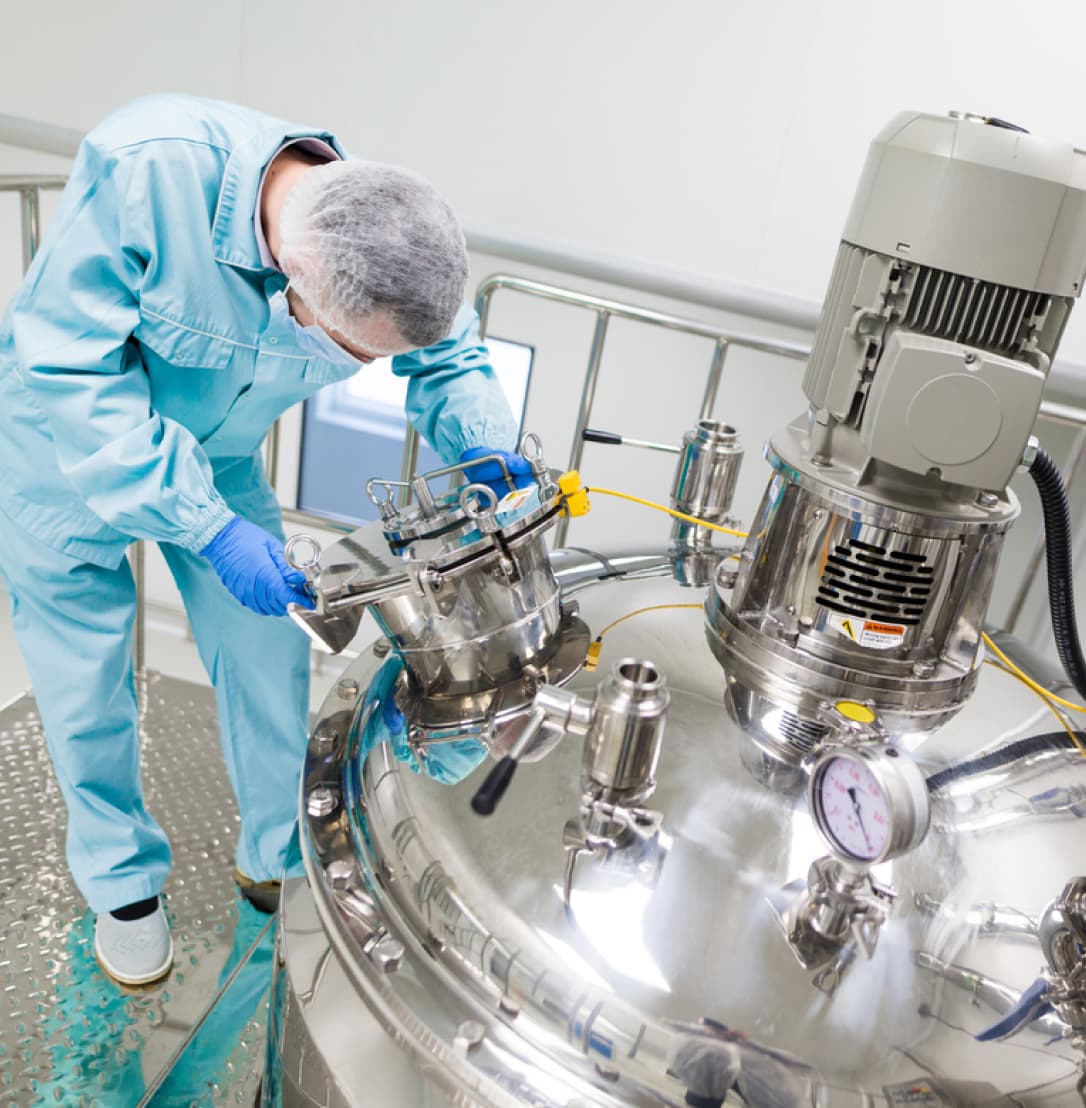
Now Complexity Can Be Your Competitive Edge
The Medical Device industry builds many critically complex, intricate and complicated products while being challenged by pressures of cheaper, faster, safer and better innovation. Shifting global supply chains and labor talent challenges make the complexity even greater. Solumina gives you the control and visibility needed to deal with these pressures while accelerating throughput, time to market and profitability.

Integrate Quality Management At All Operations Points
Cost tradeoffs between how much is spent on prevention versus fixing quality failures is a constant in manufacturing environments. Our integrated Enterprise Quality Management System helps you take early action, lowering total cost of quality by reducing defects. Embedded quality control throughout the process leads to more ownership of quality by production personnel, speeding up operational efficiency.
Benefits Of Solumina For Medical Devices
The Solumina platform provides an innovative approach to simplifying how complex manufacturing, quality, and MRO processes are managed and improved to accelerate Industry 4.0 and Smart Manufacturing strategies.
Ensure Compliance
eDHR
Built-in Quality
Full Traceability
Error Reduction
Auditing & Reporting
Learn What Solumina
Can Do for You With a Custom Demo