An iBase-t MES/Quality Customer Success Story
INTRODUCTION
At Lockheed Martin’s Clearwater plant in Florida, quality management is not just about compliance to industry and customer requirements—the team has a continuous improvement culture that has led to impressive results, awards, and recognition from its customers. The continuous improvement efforts in the plant range from information systems for paperless operations and data collection to improved clean manufacturing cells to the development of high-quality inspection systems. The success of this plant over the last ten years is a great example of how strategic investments coupled with a corporate culture of continuous quality improvement yields real results.
Visitors are highly unlikely to spot a problem on the shop floor, as even external auditors are hard-pressed to locate problems at this plant. Quality is not just a buzzword at this plant. From its employee-friendly policies to quality control technologies, the plant is constantly moving forward.
THE COMPANY
The Clearwater facility is part of Lockheed Martin’s Rotary and Mission Systems (RMS), formerly referred to as their Maritime Systems and Sensors (MS2) operations, headquartered in Bethesda, MD. The division’s products include aeronautics, space systems, information systems and global services, and electronic systems. MS2 includes surface, air, and undersea applications on more than 460 programs for U.S. military and international customers.
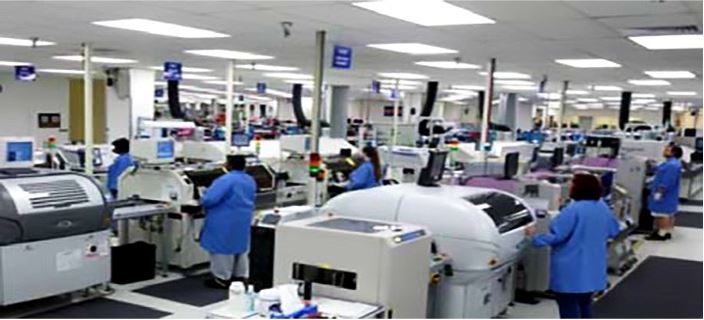
Clearwater has more than 400 employees, more than 500 suppliers, and produces a low-volume high-mix of ruggedized, high-reliability electronic data and signal processing equipment.
THEIR SOLUTION
Lockheed Martin’s MS2 Clearwater facility uses iBase-t’s Manufacturing Execution System (MES) with its embedded Quality Management System (EQMS) which enables:
- Integrated production and quality assurance across operations
- Real-time Statistical Process Control (SPC)
- Six Sigma and yield metrics used in team reviews
- Documentation of Root-Cause Analysis and Corrective Action procedures
- Performance metrics used in management reviews
Data is collected at inspection and test operations in their iBase-t MES, which alerts immediately on outof-control conditions. Other statistics like defects per million opportunities (DPMO) and yield are monitored and used to establish process improvement goals. Process improvements are standardized in the manufacturing instructions. The result is a closed-loop system of continuous improvement.
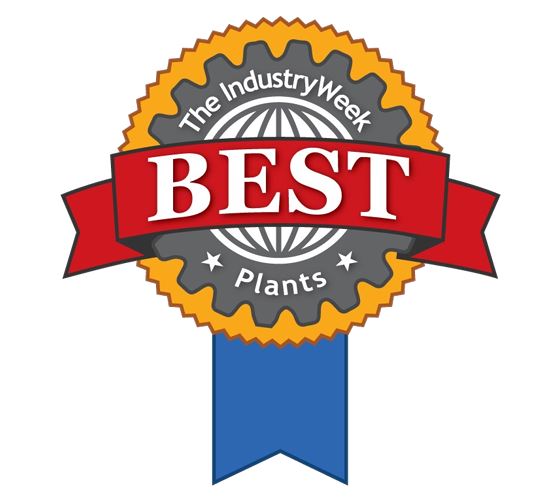
LOCKHEED MARTIN’S PRODUCTS
Lockheed Martin manufacturers a wide product portfolio, including advanced processing equipment, mission computers, communications equipment and signal processors―products that go into sea, air, ground, and space. Lockheed Martin supplies products to almost every single branch of the military including the U.S. Navy, Air Force, Army, Marine Corps and Coast Guard—along with the Department of Homeland Security and various international customers.
It is a challenge to produce this variety of products for more than 30 different programs and more than 20 customers with stringent specifications, regulatory compliance requirements, fluctuating schedules, and demands that are constantly evolving for these made- to-order products.
The management team at Clearwater is constantly investing in personnel and technology not just to save money but to achieve quality beyond the levels demanded by its market and customers. In the last 10 years, the plant’s focus on quality has resulted in a 97 percent reduction in defects. Yet, no one seems satisfied. The mindset of continuous improvement is found at all levels
A CULTURE OF CONTINUAL IMPROVEMENT
A slowdown in demand during the 1990s was a wakeup call for the management team which decided to improve performance to stay competitive and win more business. A culture of quality excellence and continuous improvement developed from these efforts and is now present at all levels of the company. Though the plant excels in quality today, employees continue to embrace change and have a desire to keep improving.
Lockheed Martin’s quality and mission success objectives include achieving balanced scorecard measurements of product quality at a sigma level of 4.85, 100 percent mission success milestones, 100 percent LM21 leadership participation, and 98 percent on-time delivery rate; as well as to maintain AS9100 certification, and several preferred supplier status awards. The Clearwater plant has been consistently achieving all these goals.
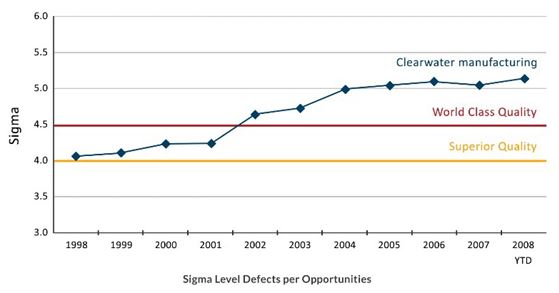
Best practices at Lockheed Martin include the LM21 Operating Excellence program. This combination of the Toyota production system, Lean Manufacturing and Six-Sigma is driving continual process improvements. LM21 is used on large-scale projects and in the facility’s daily operation, particularly on the production floor. In addition, more than 10 percent of the workforce has been certified as Six-Sigma Black and Green Belts. There is a Yellow Belt program to engage work cell teams and mentor new “quality belts”. Since its inception in 2005, the Yellow Belt program has been a huge success in the facility.
Other best practices are monthly, quarterly, and yearly performance reviews. Every year the management team reviews metrics including supplier performance, Lean and Six- Sigma manufacturing goals, test yields, customer acceptance, and field performance. Metrics establish benchmarks and goals for improvement for the following year.
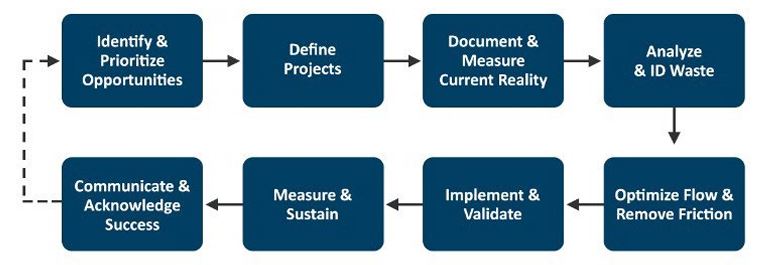
In today’s competitive manufacturing environment, gathering and analyzing metrics is not a luxury, but a necessity. The management team knows that it must remain competitive, not only against U.S. companies, but also against foreign competitors.
EMBRACING TECHNOLOGY FOR IMPROVEMENTS
Technology investments are an important factor to achieving higher quality levels. For example, Lockheed Martin implemented iBase-t’s Manufacturing Execution System (MES) to streamline and remove paperbased procedures on the shopfloor. Performance and quality data are collected in real-time as work is performed. Quality control procedures including SPC control charts are automated and immediately flag out-of-control conditions for the mechanic. Nonconformance and corrective action procedures are automatically triggered and routed for disposition. This type of closed-loop quality system is essential to achieving higher levels of quality while improving cycle time and assuring regulatory compliance with AS9100 standards. Metrics are reviewed daily and weekly at each work center to identify potential areas for improvement.
Even though there are so many different parts produced, 63 percent of manufacturing work orders build a quantity of one. The MES facilitates the flow of all these work orders and products through the shopfloor and provides real-time visibility of the work in process. The MES tracks each activity as skilled mechanics and machines hum along in a spotless environment, making meticulous movements to fasten microchips the size of a speck of pepper onto newly imprinted circuit boards.
Other examples of technologies driving quality control to new levels include improved clean manufacturing cells, enhanced parts cleaning equipment, the development of high-quality inspection systems including X-ray and optical inspection, along with a selective solder machine and automated solder robot, which eliminate much of the manual labor that was required to make precise electrical connections.
RESULTS
Lockheed does regular internal audits and external ones by certified AS9100 auditors from National Quality Assurance (NQA). The plant often scores perfect in audits with zero nonconformances. Sigma levels are often only one defect for every 10,000 opportunities in a year. The company has achieved 46.9 percent reduction in scrap/rework costs.
The company was honored by Industry Week as one of ten Best Plants for their continuous pursuit of excellence and the results of the introduction and integration of leading-edge technologies. Among the Industry Week’s Best Plant winners, the median finished- product first-pass yield was 98.6 percent, on- time delivery was 99 percent, and reduced scrap and rework cost was 33.9 percent for the three preceding years. The company has also been recognized by Quality Magazine with a Quality Plant of the Year Award in the large plant division.
The plant has not only retained 100 percent of its existing customers but has continued to add new customers. Clearwater Operations achieved the Silver Supplier Certification award from the Boeing Preferred Supplier Certification Assessment Team. The plant had achieved a 99.8 percent delivered quality level and 100 percent on- time delivery level. Less than 1.5 percent of Boeing’s electronic suppliers receive the silver or gold rating. The company has also received Northrop Grumman’s Platinum Source Preferred Award.
ABOUT iBase-T
Headquartered in Foothill Ranch, California, iBase-t simplifies complex manufacturing. Its solutions replace disparate production, quality, and MRO applications with paperless, digitally integrated solutions. The iBase-t Digital Operations Suite synchronizes data and processes to foster collaboration by establishing and maintaining a digital thread that spans enterprise systems to internal and external teams. From process and inspection, planning to the shop floor, and the execution of sustainment activities, iBase-t’s proven, pre-configured, and out-of-the-box solutions deliver real-time visibility and control that accelerates manufacturing performance.
The iBase-t Digital Operations Suite comprises a portfolio of Model-based Manufacturing applications that includes iBase-t’s Manufacturing Execution System (MES), Supplier Quality Management (SQM), and Maintenance, Repair, and Overhaul (MRO) solutions. This digital suite connects the shop floor to the top floor to ensure high quality, consistent practices, continuous product and process improvement, and embedded compliance with process standards including ISO 9001, ISO 13485, AS9100, and FDA’s 21 CFR Part 11 and Part 820.
With 30+ years of experience in highly engineered, regulated industries, iBase-t simplifies the complex by empowering customers to gain real-time visibility, take control, and drive velocity across their operations.
The iSeries, powered by the Solumina platform, has a cloud-native microservices architecture with open APIs that extends a digital ecosystem to drive innovation, simplify hardware and software systems integration, and deploy advanced technologies. iBase-t works closely with many industry leaders, including Lockheed Martin, Northrop Grumman, Rolls Royce, Pratt & Whitney, and Textron.