What Is Paperless Manufacturing?
Paperless manufacturing uses digital technology to connect all the people, parts, equipment, and processes related to the shop floor. Instead of exchanging paper, emails, and spreadsheets, everyone involved uses an integrated software application that makes communication virtually automatic and instantaneous across operations.
Digital Work Environment
From digital work instructions on the production line, to real-time reports in the executive office, a paperless shop floor system breaks down silos and provides the information people need when they need it. It improves the speed and accuracy of everything a manufacturer does.
With the right platform, paperless systems can be extended across the value chain to include suppliers, partners, and even customers.
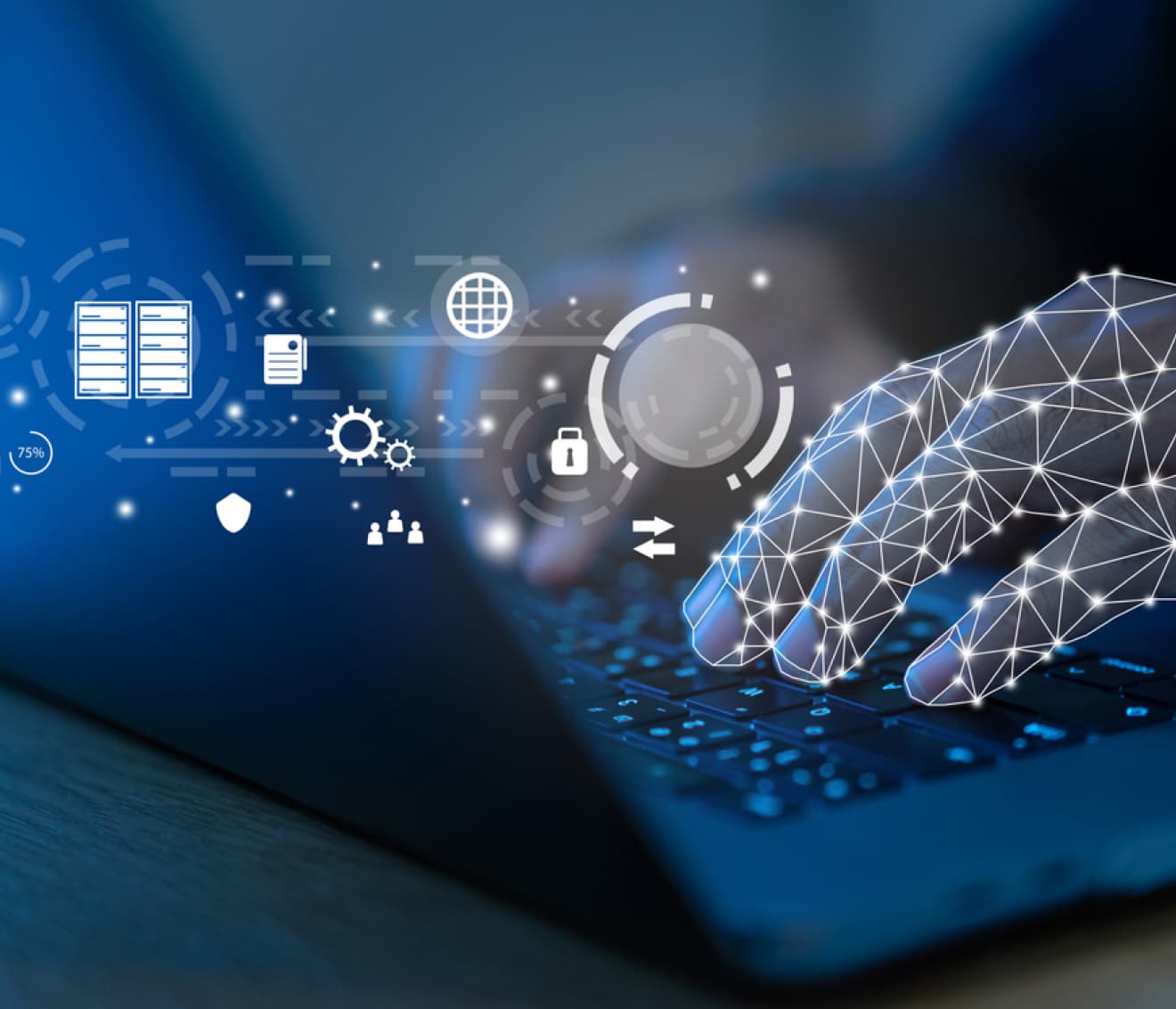
The State of Paper-Based Manufacturing
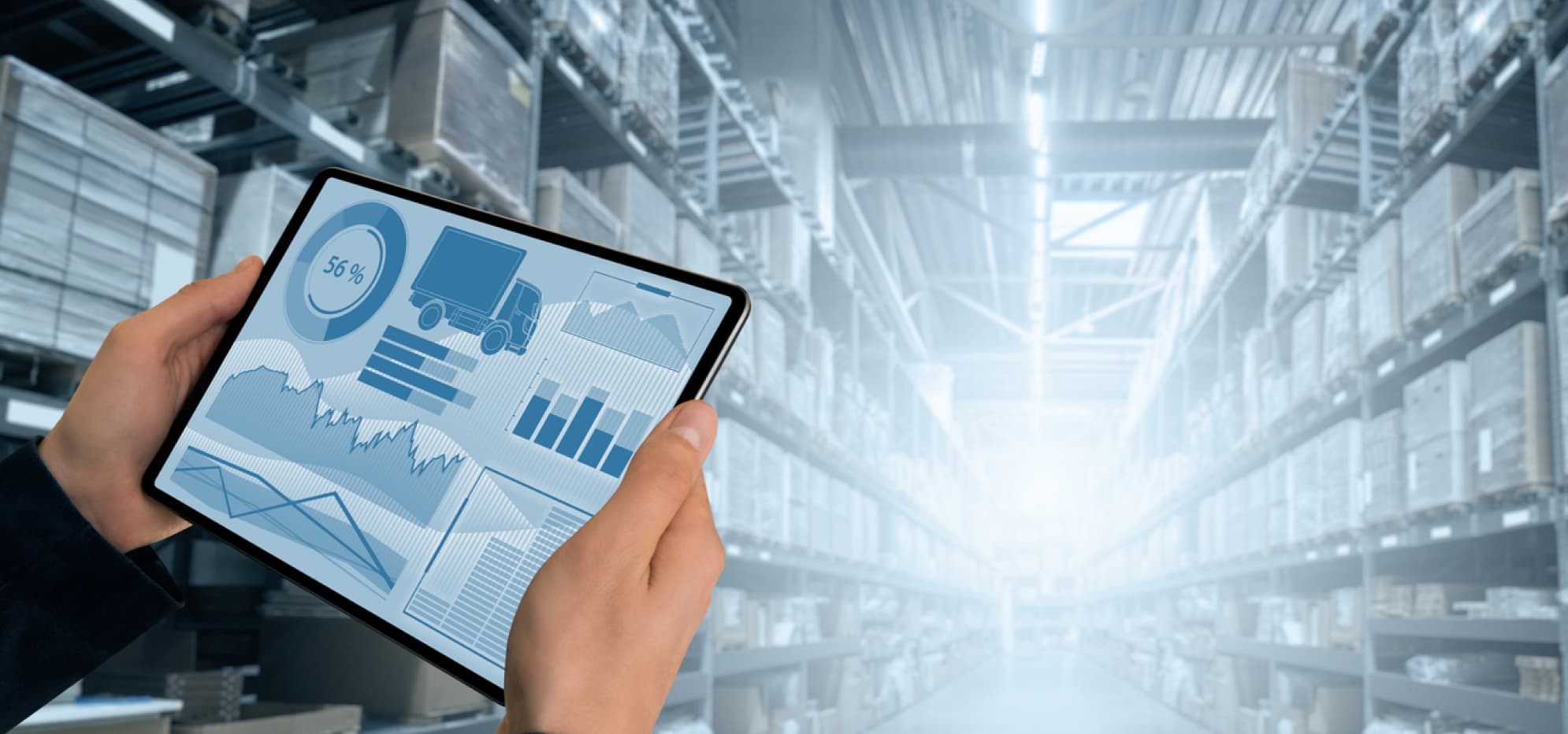
Managing production processes with paper is as old as manufacturing itself, so it’s no surprise that many manufacturers are still using paper (or emails) to perform critical steps like issuing work instructions, process planning, and producing reports for management.
But what used to be acceptable no longer is. Paper is costly, slow, cumbersome, and prone to error. Meanwhile, the pace of change in the world keeps accelerating. Manufacturers are going paperless to solve a host of problems caused by outdated paper systems.
Which Manufacturers Can Go Paperless?
Until recently, paperless manufacturing software was only practical for large manufacturers because of the costs and resources needed to support it. That’s no longer true, as modern technologies and cloud-based software are making paperless manufacturing a reality for companies of all sizes, from a single plant to a global enterprise.
Common Disadvantages of Paper-Based Operations
Supply Chain Weakness
Supply chains that operate on paper and emails are slow to adjust yet supply chain disruptions are a regular occurrence for many firms.
Losing Talent
Paper-based companies are at a disadvantage. The younger workforce has grown up with digital technology and prefer companies that use it.
Compliance Risks
Compliance is a complex task for manufacturers. Paper-based manufacturing is prone to error that can lead to non-compliance issues.
Lost Paperwork
Delayed or lost paperwork can lead to a number of issues, including production problems downstream.
Change Delays
Changes are slow and costly with paper. Simple work order edits can take hours/days to execute, as partners and suppliers must be notified.
Human Error
Paperwork required for manufacturing means human error is unavoidable. In regulated and critical industries, this risk is not acceptable.
On-demand Webinar
The hidden costs of paper
The True Cost Of Paper Is Crippling Manufacturers
The real cost of paper is not just the money spent, but the opportunities lost. The average company spends one to three percent of its revenue on printing costs alone. (Gartner)
Paper Slows Down Business
Paper Has “Blind Spots”
Paper Is Not Secure
Paper Systems Reduce Your Revenue
What Does Paperless Manufacturing Software Do?
What exactly does paperless manufacturing do? Essentially, paperless manufacturing provides a unified software application for planning, executing, monitoring, and reporting on every step of production.
To do all of this, paperless manufacturing provides at least three essential functions.
Manufacturing Execution System (MES)
MES is the central nervous system of a paperless operation. It executes and monitors all work-in-process on the shop floor and provides real-time visibility of production activities. It tracks and documents the transformation of raw materials through finished goods, coordinates activities such as scheduling and dispatching, and integrates with other corporate systems like PLM and ERP.
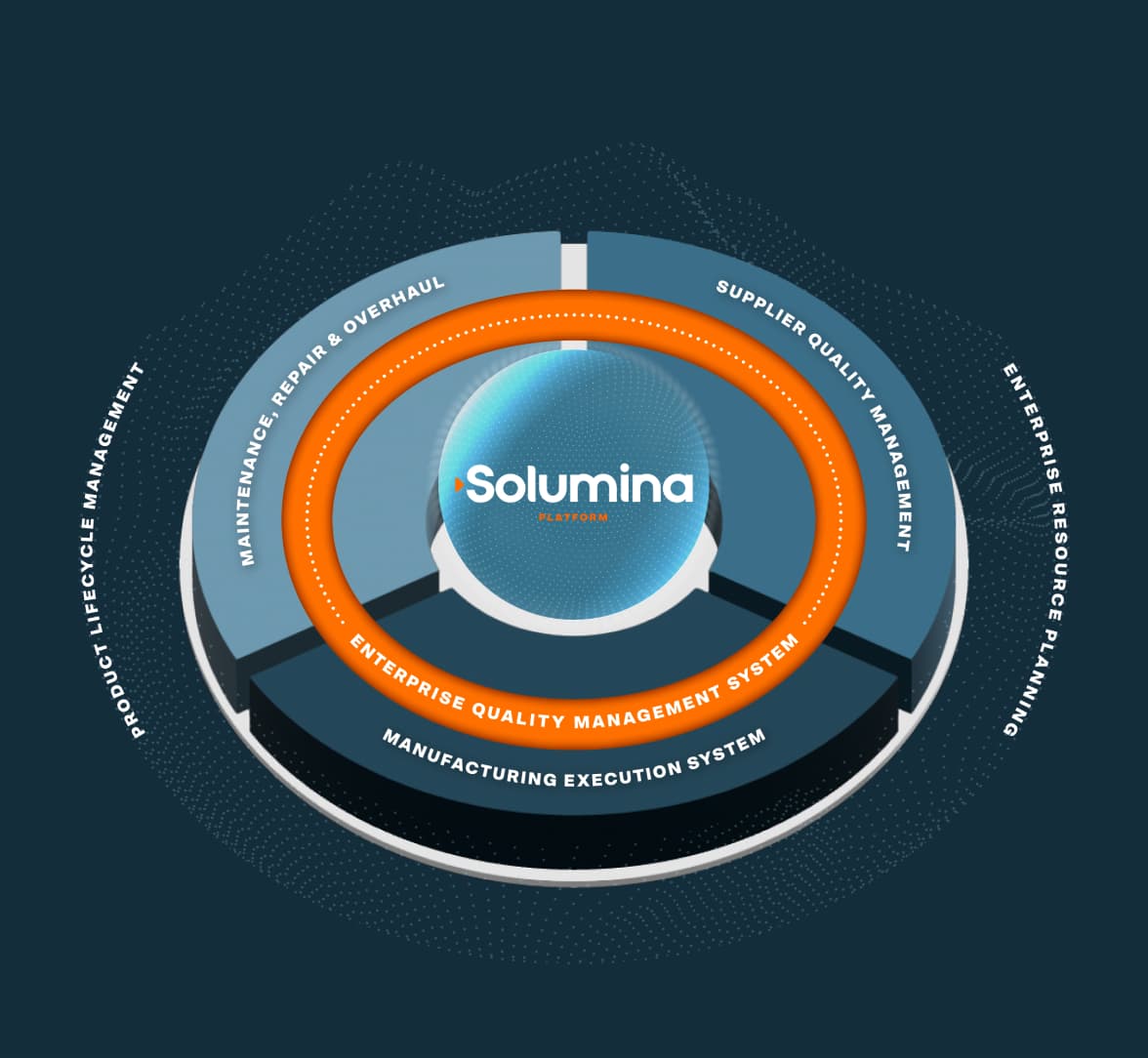
MES should also provide real-time manufacturing intelligence for decision-makers. Unlike the information in paper systems, digital information can be instantly gathered, analyzed, and delivered to whoever needs it.
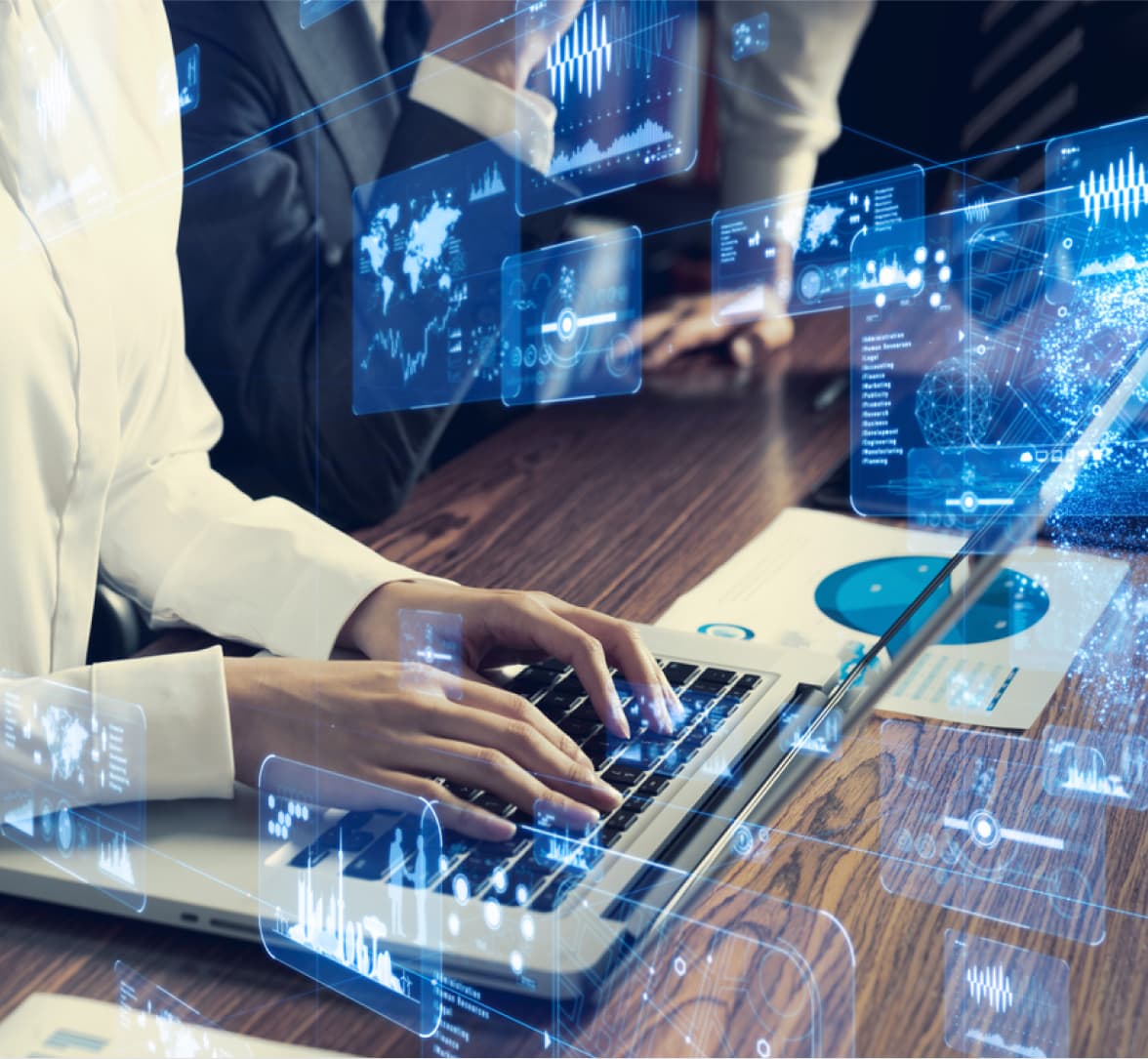
Digital Process Planning
Transitioning from engineering to manufacturing BoM is an error-prone process. Digital process planning ensures your shop floor instructions are updated to all engineering changes. The result is more consistent results from your production lines by ensuring everyone in your company is designing and producing based on the same information.
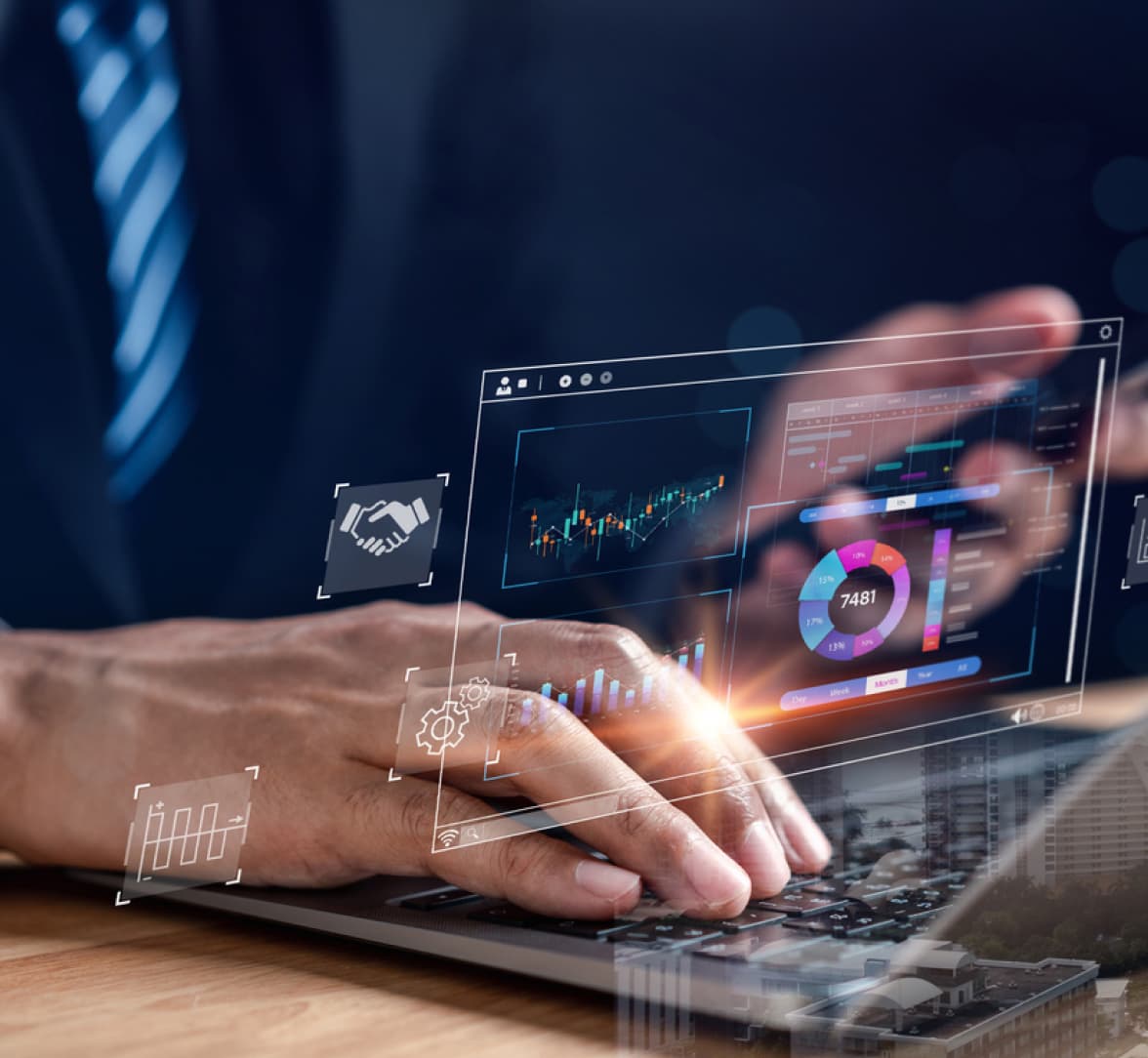
Digital Work Instructions
Digital work instructions make sure that everyone in the plant gets the latest work instructions. These instructions can include engineering drawings, photographs, videos, or any other documentation. It’s all distributed instantly to every workstation, where the MES can verify that the instructions are received and enforced.
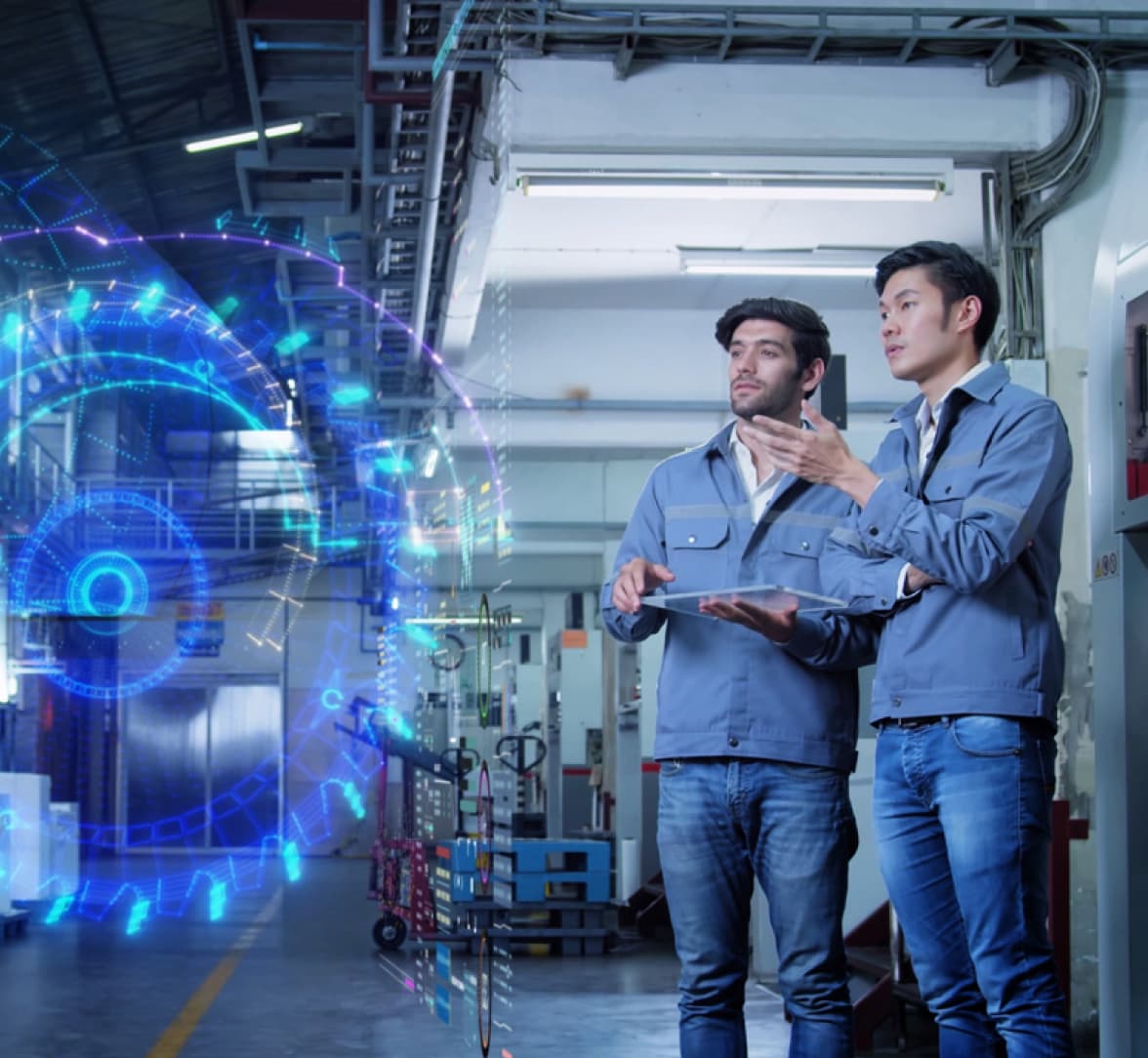
Adding MRO and SQM
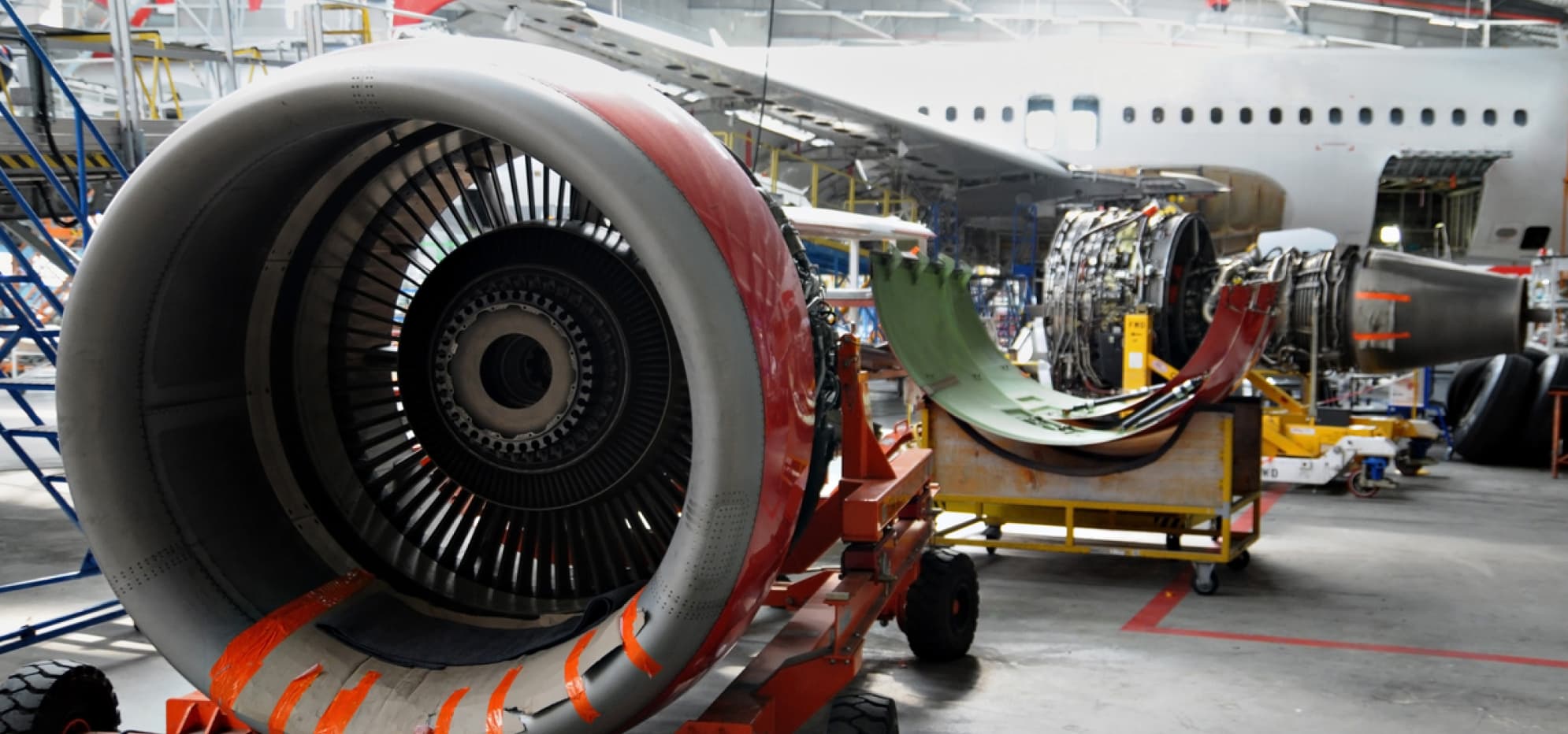
iBase-t also goes a step further by offering paperless Maintenance, Repair & Overhaul (MRO) and Supplier Quality Management (SQM) to its integrated suite of solutions, enabling manufacturers to connect more of their operations. Our MES, MRO, and SQM solutions can stand alone, but the benefits are amplified when they are used together, providing a more complete picture of operations.
- SQM – Are your suppliers hurting your business or enabling its success? Digital SQM helps manufacturers answer that question by providing a systematic way to measure and validate supplier quality.
- MRO – Digital MRO schedules and manages repairs in a consistent, repeatable way to minimize risk and downtime. It increases visibility, control, and efficiency of your MRO operations.
Benefits of Paperless Manufacturing
Better Control Over Production
Traceability and Employee Accountability
Manage Engineering Change Orders
Fewer Defects and Higher Quality
Increase Productivity
Document Institutional Knowledge
Specific Personnel Sign-Offs with User-Based Permissions
Attract the Next Generation of Workers
By 2024, half of factory work will be performed remotely as manufacturers search for new ways to innovate.
Gartner
What Can You Expect From Paperless Manufacturing?
Faster NPI
Closed-loop Manufacturing
Cheaper and Quicker Document Compliance
Real-time Data for Informed Decision-making
Manufacturing Intelligence
Complete As-built Histories
Foundation for Digital Thread and Industry 4.0
Replace Barcoded Paper Travelers, Work Instructions and Inspection Sheets
How to Deploy Paperless In Manufacturing
There are many paths to paperless manufacturing, from buying and operating your own hardware and software, to subscribing to the capabilities you need over the cloud. Whatever the technology path chosen, manufacturers can pursue it in stages.
On-Premise
Large enterprises with deep IT resources may host manufacturing software on their own servers with an on-premise solution.
Public Cloud
This is the most affordable and scalable solution, using providers like AWS to host applications and connect users. This approach is often used by medium and smaller companies to limit their upfront capital costs and reduce the IT burden.
Private Cloud
Manufacturers with special security or control concerns can choose a private cloud, in which the servers and software are hosted by an outside firm but are used exclusively for that client alone.
Hybrid
A hybrid approach is a combination of any two of the above. For example, you might want to manage and store sensitive data on-premise and use the public cloud for less sensitive applications.
What Do the Industry Analysts Say?
25%
1 – 3%
Next Steps
Whatever the technology path chosen, manufacturers can pursue it in stages. Your vendors should be able to help you identify and address the areas that are easiest to implement and fastest to create profits. By addressing those first and building value as you go, paperless systems can pay for themselves.
Learn More About the Power of Paperless Manufacturing
Learn What Solumina
Can Do for You With a Custom Demo